Product Code: ICA11_M1301
From Cw to Fs: Fiber Lasers in Medical Device Manufacturing
Authors:
Roland Mayerhofer, ROFIN-BAASEL Lasertech GmbH & Co. KG; Starnberg Germany
Dieter Mairhoermann, ROFIN-BAASEL Lasertech GmbH & Co. KG; Starnberg Germany
Michael Mueller, ROFIN-BAASEL Lasertech GmbH & Co. KG; Starnberg Germany
Markus Roehner, ROFIN-BAASEL Lasertech GmbH & Co. KG; Starnberg Germany
Stephan Geiger, ROFIN-BAASEL Lasertech GmbH & Co. KG; Starnberg Germany
Ronald Holtz, LASAG AG; Thun Switzerland
Christoph Ruttimann, LASAG AG; -
Presented at ICALEO 2011
Since decades, lasers are a well-established tool in development and production of medical devices. Here, analogue to other industrial application areas, fiber lasers are gaining a significantly increased market share amongst the different laser concepts. Typical applications of lasers in medical device manufacturing comprise cutting, welding, surface structuring and marking processes.
Manufacturing of medical devices from tube material (i.e. stents) is one of the prominent laser cutting applications in the medical device industry. For years, production relied on laser fusion cutting with lamp-pumped solid state lasers, providing pulse widths in the µs-range. Newly developed modulated fiber lasers with peak power levels above 1 kW have substituted lamp-pumped lasers for that application area. But even with an optimum setup, fusion cutting processes are not completely free from burr and recast formation inside the tube. Therefore, post-processing steps are necessary, including brushing and chemical etching in order to remove oxide layers as well as electrochemical polishing to round-off edges. Whereas such post-processing methods are tolerable for standard materials like stainless steel and cobalt-chromium alloys, sensitive materials, like the shape memory alloy Nitinol, are prone to chemical and mechanical damage. Here, the use of ultra short pulsed fiber lasers is a viable way to significantly reduce heat affected zones and melt generation and thus eliminating recast layer and burr formation.
Whereas for metal stents ultra short lasers are still in competition with modulated-cw fiber lasers, there is no other way to cut bio-absorbable polymer materials, like polylactic or polyglycolic acids. Suffering from low melting temperatures, low absorption and low heat conductivity, machining of those materials with traditional cutting lasers is impossible. Microstructural changes cannot be tolerated, as they would not allow for the necessary precision and mechanical properties of those implants. Here, femtosecond lasers already have achieved excellent results with vascular stents showing high-precision cuts with perfect edge quality.
Also, for metal welding applications on medical devices like endoscopes, probing devices or surgical knifes, fiber lasers are prepared to substitute lamp-pumped Nd:YAG lasers on the long run. There are two different approaches to do that: seam welding with cw-fiber lasers using different concepts to enlarge the weld pool size or spot welding with kW-pulsed fiber lasers.
The presentation will give an overview on the variety of fiber laser applications in medical device manufacturing, covering standard fusion cutting with modulated fiber lasers, the specifics of cold processing with ultra short pulsed fiber lasers as well as the characteristics of fiber laser welding.
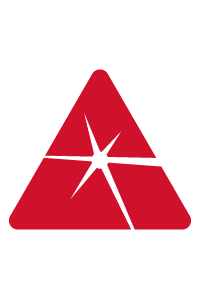
$28.00
Members: $28.00
Note: When applicable, multiple quantity discounts are applied once the items are added to your cart.