Product Code: JLA_5_1_33
Authors:
Mingli He
P. J. Bishop
A. Minardi
University of Central Florida
High power lasers are used in industry as machining tools for many operations including drilling, cutting, welding, and etching. Because of its advantages over conventional machining such as tight tolerances, ability to machine hard materials without wearing of the machine tool, and ease of automation, an experimental and analytical study was undertaken to investigate the feasibility of the laser to cut a nearly pure fibrous ceramic used as insulation material on the Space Shuttle. An analytical model was developed for drilling using a spatially varying laser beam. The model was used to determine the energy delivery to the surface from the laser beam and the conduction within the solid ceramic. A similarity variable was introduced to solve the transient heat conduction equation inside the solid tile and predict the temperature and temperature gradient. The temperature distribution within the tile was found and then used with an assumed boundary condition to predict the drilled cavity shape. This model has been used to develop algorithms for input into a computer automated laser machining facility. The model has been compared to experimental data taken using the ceramic material. The cavity shape and depth were experimentally measured in a thick sample using a CO2 laser and 10:5 collimation. Holes were drilled for various laser powers and exposure times. The hole depth and radius were measured after cross‐sectioning the samples. Model predictions were within 15% of experimental results.
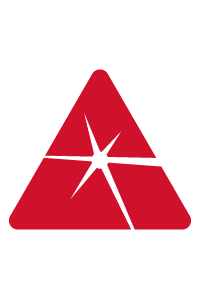
$25.00
Members: $25.00
Note: When applicable, multiple quantity discounts are applied once the items are added to your cart.