Product Code: JLA_4_2_15
Authors:
Angel L. Ortiz
General Electric Corporate Research and Development, 1 River Road, P.O. Box 8, Bldg. KWC‐617, Schenectady, New York 12301
A high power Neodymium: Yttrium‐Aluminum‐Garnet (Nd:YAG) Total‐lnternal‐Reflection Face Pumped Laser (TIR‐FPL) coupled with a fiber delivery system has been proven to be a powerful processing tool for On‐The‐Fly (OTF) drilling [1–3]. Single‐Pulse OTF drilling, (i.e., one laser pulse per hole with continuous part motion) at shallow angles to the surface with material thicknesses up to 50 mils can be easily accomplished generating good quality holes. Optical sensors are used to determine laser pulse break‐through time and are examined as a potential feedback method for a drilling process monitor. The OTF samples are subjected to flow measurements to determine trends based on laser parameters (laser pulse energy and focal point location on the part). The primary findings are that optical break‐through sensors provide a viable monitor of optical system behavior to control the laser drilling process. The percent Break‐Through Time (%BTT) defined as the ratio of the breakthrough onset time divided by the total laser pulse duration decreases with increasing laser pulse energy. A 34% variation in the average flow per hole (defined as the total coupon flow/total number of drilled holes) on the OTF drilled part can be obtained by controlling the focal point placement on the part and changing the laser energy per pulse. These data offer information about the characteristics and process capabilities of FPL/fiber delivered laser beams used in manufacturing applications, specifically, OTF drilling capability with fiber delivered laser beams, and the control of airflow on an aircraft engine part.
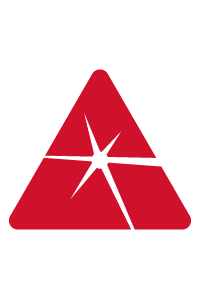
$25.00
Members: $25.00
Note: When applicable, multiple quantity discounts are applied once the items are added to your cart.