Product Code: JLA_18_2_161
Authors:
D. Triantafyllidis
Laser Processing Research Centre, School of Mechanical, Aerospace and Civil Engineering, The University of Manchester, Manchester M60 1QD, United Kingdom and Corrosion and Protection Centre, School of Materials, The University of Manchester, Manchester M60 IQD, United Kingdom
L. Li
Laser Processing Research Center, School of Mechanical, Aerospace and Civil Engineering, The University of Manchester, Manchester M60 1QD, United Kingdom
F. H. Stott
Corrosion and Protection Centre, School of Materials, The University of Manchester, Manchester M60 1QD, United Kingdom
Laser surface treatment of ceramics by melting and resolidification generally leads to the formation of fully densified and homogeneous surfaces, with enhanced mechanical and physical properties. A common problem associated with the process is the formation of thermally induced cracks on solidification and cooling. This, however, can be eliminated by controlling the cooling rates and thermal gradients during processing. Such control can be achieved by applying pre- and postheating methods or by scanning the laser beam at relatively slow speeds to modify the thermal shock conditions to which the surface is subjected. The latter technique has been successfully applied to the development of crack-free surfaces in Al2O3-based refractory ceramics. The relatively slow speed, however, limits the practicability of the technique. This article presents a novel theoretical analysis of the effects of various nonconventional beam geometries on cooling rates and, hence, on interaction times and processing speeds, during laser surface treatment of ceramics. Initially, a commercial finite element analysis package was used to simulate the material-beam interaction conditions for various beam geometries, including rectangular, line, triangular, pi, and rhomboid. The cooling rates associated with these beam geometries were assessed and compared with those for the standard circular beam geometry. The model predicted that the rhomboid and pi beam geometries result in lower cooling rates, the line beam geometry in higher cooling rates, and the rectangular and the triangular beam geometries in similar cooling rates to those of the circular beam geometry. In particular, the model predicted that the processing speed for the rhomboid geometry had to be increased by a factor of about 5 and that for the pi geometry by a factor of about 2.5 compared to the standard circular beam geometry to produce similar cooling rates.
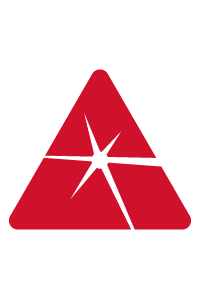
$25.00
Members: $25.00
Note: When applicable, multiple quantity discounts are applied once the items are added to your cart.