Product Code: ICAL08_102
Novel Computer Generated Diffractive Optics Modifying Beam Characteristics to Improve the Microstructures of Directly Deposited Inconel 625
Authors:
John Tyrer, Loughborough University; Loughborough Great Britain
Matthew Gibson, Loughborough University; Loughborough Great Britain
Rebecca Higginson, Loughborough University; Loughborough Great Britain
Presented at ICALEO 2008
A major use of metal additive welding is the repair of damaged or worn turbine blades. Current methods used to produce multiple layer repairs in high nickel content alloys have shown an inability to prevent intergranular cracking and levels of porosity in the deposited material. These problems are caused by the intense temperature gradients induced by circular beam shapes. When a laser beam is scanned across a workpiece the shape of the beam as well as the flux distribution will cause a temperature gradient to form across the weld pool. High thermal gradients lead to the growth of weak microstructures, along with high thermally induced stresses during and after the processing. In Inconel 625 there is a region of 700C between a molten state and boiling of the alloy constituents. The temperatures present in traditional beam profiles may lead to boiling of the material at the centre of the weld. These extremes of temperature will typically cause upwards of 1% porosity and alloy constituent migration. This paper looks at a number of beam intensity profiles made using a novel beam shaping method. Computer generated diffractive optic elements (DOE) developed at Loughborough University have been shown to reconstruct a laser beam intensity profile into any user defined structure with typically 90% efficiency. A number of different beam profiles have been used to reduce the temperature gradient across the weld pool, removing overheating of the weld pool centre. This has shown to have had a dramatic positive effect on the deposition microstructure, by reducing the average grain size, promoting grain growth directions, crystal solidification orientations and a removal of deposition porosity. Having seen the improvements made by changing the beam shape, an ideal beam distribution was established for the metal additive processes. Through the use of thermal modelling, the temperature field required in the weld pool was determined and back propagated to the surface to find the beam flux distribution required. The complexity of the resulting beam, is not intuitive and can only be achievable using a DOE. Electron Back-Scatter Diffraction (EBSD) has been used to characterize the grain properties of the resulting depositions. Tailored beam profiles show improvements in the mechanical and corrosion properties of the depositions, when compared to welds using Gaussian and uniform circular beams. Energy Dispersive X-ray spectroscopy (EDS) has been used to show a reduction in the segregation of the alloying elements in depositions. Using these methods multiple layer welds of crack sensitive, high nickel alloys, have been made with an absence of cracking or porosity.
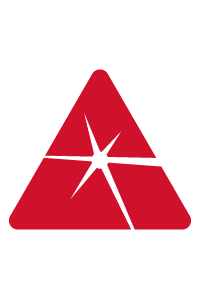
$28.00
Members: $28.00
Note: When applicable, multiple quantity discounts are applied once the items are added to your cart.